Top 10 most common Hazards and associated risks in the workplace
MAKROSAFE have been assisting clients for more than 23 years with the identification of hazards, CONTACT US now to assist you finding at least 10 hazards in the workplace.
There are hundreds, if not thousands, of possible hazards in the workplace. Some industries naturally carry more risks, but we have outlined the top 10 most common workplace hazards and asssociated risks that pose a threat:
- Hazardous chemicals, which include the following: acids, caustic substances, disinfectants, glues, heavy metals (mercury, lead, aluminium), paint, pesticides, petroleum products, and solvents.
- Ladders. All plants and warehouses use ladders constantly, and 8 percent of all occupational fatalities are caused by falls. Download your FREE Ladder Inspection Checklist
- Scaffolding hazards. This includes planks giving way or breaking, employee negligence, and falling objects.
- Vehicle accidents. This includes industrial trucks, golf carts, cars, etc.
- Respiratory hazards. These risks are applicable when welding, for example. Unhealthy breathing environments include insufficient oxygen, vapours, gasses, fibreglass, and dust.
- Electrical wiring and systems that can cause electrocution or fires.
- Unexpected start-up or malfunction of machinery and equipment.
- Falling objects from shelves, higher floors, or scaffolding.
- Slippery and wet floors that cause slips and falls.
- Objects on the ground or in doorways, including wires and cords, which result in trips, falls, lacerations, and bruises
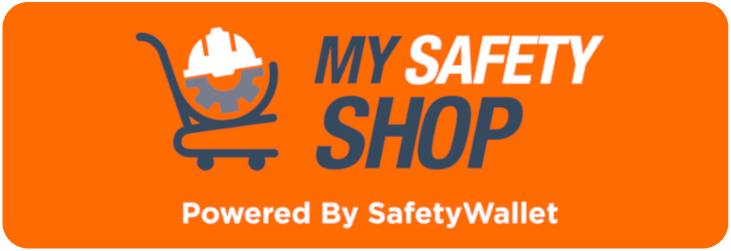
A Risk Assessment is the first step to identify your hazards in the workplace.
WHAT IS A TASK RISK ASSESSMENT (TRA)?
This risk assessment is conducted by a competent person to determine the hazards and risks associated with a specific task that is being performed. Using a standardised methodology, tasks are placed into a task inventory and potential hazards that may be encountered while performing each task are identified. Their associated risks are determined and quantified to determine their level of risk. Control measures are then determined that, when implemented, will mitigate and reduce the level of risk for each task to an acceptable level.
Based on their level of risk, the tasks are then arranged in the task inventory according to their level of risk from highest risks to lowest risks.
Through the re-arrangement of the quantified tasks, the employer can now concentrate on implementing the control measures for each task, prioritising their efforts on the tasks that pose the greatest risk to health and safety and then working down the task inventory to the tasks which pose lessor risks to health and safety.
WHO NEEDS TO DO THIS?
This task risk assessment is intended for all companies who are required to conduct a risk assessment within their organisations.
WHY IS THIS RISK ASSESSMENT IMPORTANT?
This task risk assessment is important because it determines hazards and their associated risks in the workplace. At the same time, it quantifies these to determine how much risk they represent to the organisation and its operations and details the relevant control measures that need to be put into place in order to ensure that the level of risk is an acceptable one. This provides evidence to an inspector that a risk assessment has been conducted by the organisation and that the organisation has made a comprehensive evaluation of the hazards and risks within its workplace. A risk assessment is mandatory under section 8(2)(d) of the Occupational Health and Safety Act 85 of 1993 and its availability shows that the employer is complying with this legislation in respect of the risk assessment requirement.
VALIDITY
This task risk assessment must be conducted by a person who is competent to do so and who has been appointed to carry out the task.
Download free e/book : A Competent Person - The purpose of this e-book guide is to provide guidance to users (employers) on what the formal definition of a competent person is in the workplace, as determined by the Department of Employment and Labour.
The risk assessment document must be approved and signed off by top management and must be communicated to all employees throughout the organisation.
The document must be maintained and reviewed regularly so that it remains relevant and must be available to any interested parties who wish to view it.
Keeping your workplace legally Health and Safety Compliant may seem like a daunting task. At MAKROSAFE, we have an experienced team of OHS experts available to assist in keeping your company Health and Safety Compliant according to South African Health and Safety Acts and Regulations.
The MAKROSAFE Health and Safety Risk Control Package will assist you with your Risk Management Programme.
By signing up with our Health and Safety Risk Control Package, MAKROSAFE will assist you with your Risk Management journey.
Comments (14)
Thank you and much appreciated. I am studying my OHSE and I have find this information very useful and easy to understand
2024-04-16 13:45:46Hi Lovejoy We are glad to help. All the best with your studies.
2024-04-17 07:18:10Thank you so much the informative, simplified and understandable article.
2022-05-02 16:09:26Thanks for your information it’s so important to us it is definitely telling us we should avoid hazardous
2023-03-14 19:37:49Dear Tsepang Thank you for your comment, we do appreciate it... Don't forget to follow the links in the blog to get more info and look at our packages to assist you...
2023-03-15 08:43:26Nice article Thanks for sharing this informative post,Keep posting!
2022-07-01 16:08:24It is very awesome especially article facilitates all you belonging needs. Thus material is written in understandable form so that everyone can understand it easily. I will share it with others, please keep it up.
2022-12-02 09:16:58Thanks for informing us of the most common hazards in the workplace. It is useful for workers to know these hazards that may take place while working. Height safety training Mackay helps workers to understand safety precautions to protect them against hazards.
2021-06-03 04:18:24Such a great information. This is really very helpful for bloggers
2021-06-05 04:51:47identify 3 common hazards for a client in a physical health or wellbeing community organisation
2021-07-17 12:45:30Plz send me 10 health occupational hazard in different occupation
2021-03-12 07:24:56Is there only ten (10) common hazards, can affecting us?
2021-04-07 14:23:36Hazard is an dangerous event or situation that has potential to harm human,s life, properties, economies, and many more. But it has less damage in comparison to disaster.
2020-12-08 11:45:56Identify at least 10 hazards (with pictures)that may be found in the organization.
2022-06-06 09:46:27Can occupational hazard be referred to a person's mental state of mind?
2021-04-22 08:51:12It is good things what I got from lesson
2021-06-28 09:42:09I like your post a lot. I just stumbled upon your blog and wanted to say that I've enjoyed browsing your posts. I will subscribe to your feed, and I look forward to reading your next post. I highly recommended
2021-12-13 07:31:23