The Occupational Health and Safety Act 85 of 1993, Section 8 requires the employer to bring about and maintain, as far as reasonably practicable, a work environment that is safe and without risk to the health of the workers. This means that an employer needs to ensure that the company is as compliant to legislation as possible, to reduce injuries, remove hazards and make the work environment safe and healthy for employees.
It is not however, it's not only the responsibility of the employer to keep the work environment safe and healthy. Section 14 of the Occupational Health and Safety Act (85 of 1993) states that employees need to look out for their own safety as well as the health and safety of those around them. Health and Safety is therefore everyone's duty.
Here are the MAKROSAFE 21 tips for Health and Safety Compliance.
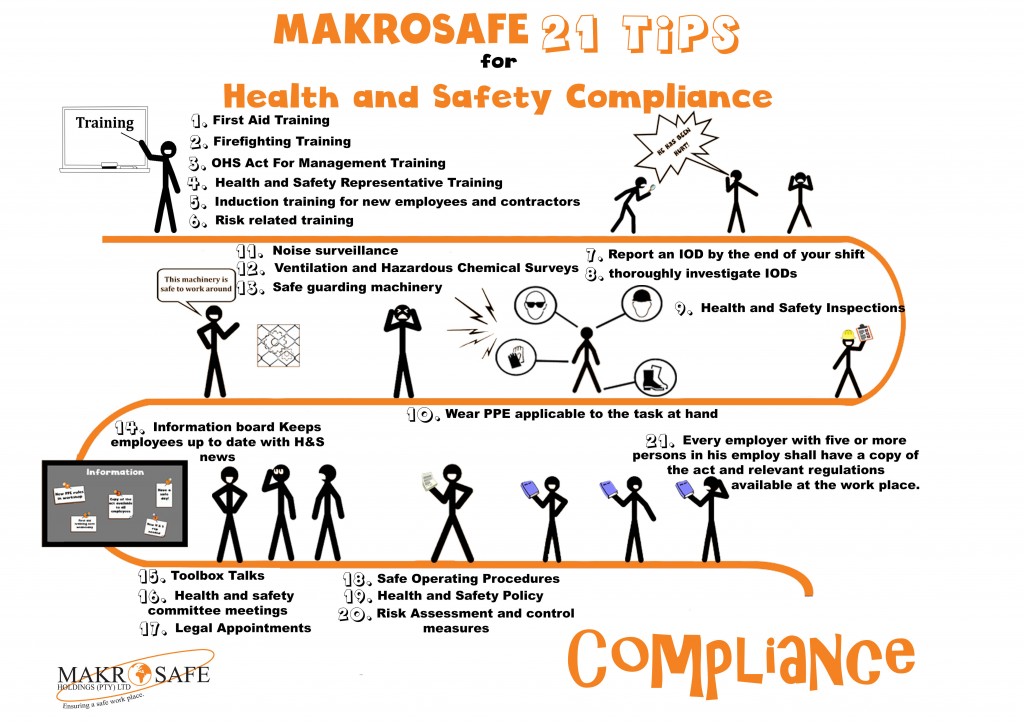
OHS Training
- At its most basic, First Aid is the initial assistance given to a victim of injury or illness. With the knowledge of First Aid, it is your duty to provide quick and effective emergency treatment until professional help arrives. First Aid Training can be useful in many situations, it increases the safety of you and your fellow employees, helps relieve pain when someone has been injured and prevents a dangerous situation from getting worse as well as improving the Health and Safety compliance of your company. MAKROSAFE'S First Aid Courses allows the candidate / delegate the opportunity to further his knowledge from Level 1, to a more advanced First Aid Level 2 and eventually to the essential lifesaving skills required from a Level 3 First Aider.
- Governments and large corporations all over the world have made Fire and Safety Training courses a key part of their workplace Health and Safety program.
The MAKROSAFE Firefighting course will help you to:
- Identify different types of fire
- Explain and practice fire prevention
- Operate basic firefighting equipment
- Perform basic firefighting procedures
- Health and Safety is the responsibility of both management and employees. Management is accountable for any form of non-compliance of Health and Safety in the workplace.
It is important to note that, while some responsibilities can be delegated, the superior remains accountable for seeing that they are carried out correctly and safely. - The Occupational Health and Safety Act 85 of 1993 aims to promote the Health and Safety of everyone at work and of other people in or around places of work. To achieve this, it is important to have dedicated Health and Safety Representatives to inspect a workplace, accompany an investigator during accident investigations, and make sure all IOD’s are reported as quickly as possible to reduce further injury in the workplace.
- Induction training is provided to new employees or contractors by the employer to help them become familiar with their environment and the people working around them. This type of training will also outline the basic overview of the business and its services as well as the new employee’s role in the environment.
- It is important for employees to undergo risk related training, to prevent injuries or death when performing hazardous jobs.
IODs
The prevention of accidents and, more importantly, the administrative follow-up with authorities is a time-consuming process which requires much attention to detail. Workers need to notify their employers of an accident before the end of their shift and employers must submit certain documents to the Compensation Commissioner within 7 days of being notified.
- The interest and the well-being of the employee as well as the continuity of the company operations, demands in-depth knowledge and understanding of the Compensation for Occupational Injuries and Diseases Amendment Act, No 61 of 1997 and the Occupational Health and Safety Act 85 of 1993. It is very important to thoroughly investigate IODs as it gives you a good idea of how the accident occurred and how to prevent it from happening in the future by removing hazards and making the work environment safer.
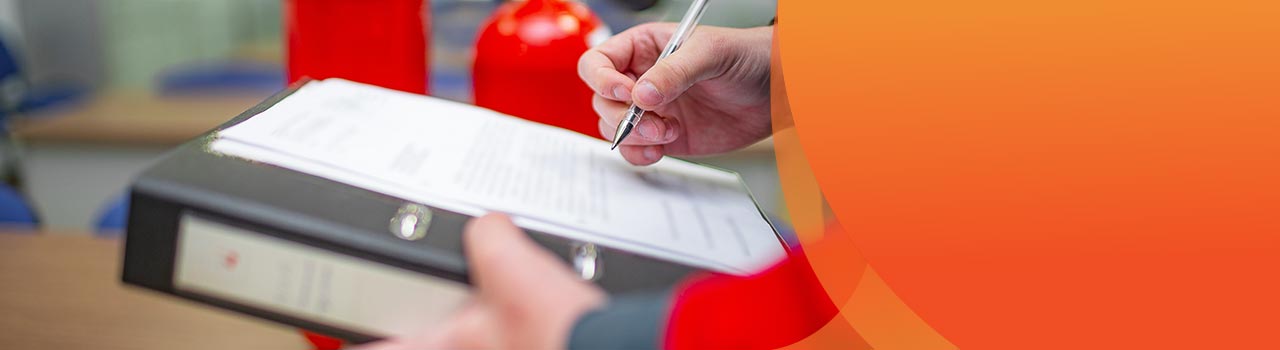
OHS Inspections
- Workplace inspections are an essential component of your prevention program. The purpose of workplace inspections are to:
- Identify and record potential hazards
- Identify hazards that need immediate attention
- Determining whether current hazard controls are effective
- Recommending solutions and corrective measures when needed
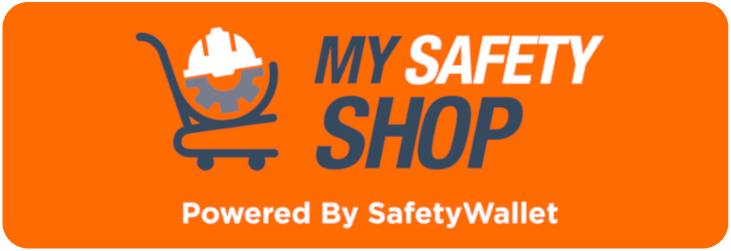
PPE
- Personal Protective Equipment (PPE) is the equipment you wear to reduce the impact to your body when an accident occurs. PPE is NOT the first line of defense against hazards in the workplace, proper Health and Safety measures need to be put into place before PPE is considered. It is also very important to wear applicable PPE to the task at hand and to look after your PPE properly to prevent injuries or occupational health issues.
Occupational Hygiene Surveys
- Loud noise at work can damage people's hearing and lead to risks to safety. You would usually start the health and safety noise survey before employees are exposed to noise, to prevent any health issues. It can, however, be introduced at any time for employees already exposed to noise. This would be followed by a regular series of checks.
- Occupational Hygiene Surveys are important to make your employees work environment less hazardous and harmful to their health by preventing occupational diseases. These compulsory surveys are an important part for your company to become compliant with the Health and Safety Legislation.
Safeguarding Machinery
- Safe guarding machinery is implemented where machinery may pose a danger to any person. The machinery must be enclosed and where the premises are unattended the premises must be kept closed and locked. By keeping machinery protected from employees, and employees protected from machinery, you can reduce the risks and injuries caused by dangerous machinery with moving parts.
Information Boards
- Information boards keep employees up to date with Health and Safety news in their departments and general working environment. By keeping employees more informed about important changes in the workplace, you can reduce the risks of Health and Safety hazards and keep them motivated to keep their workplace and surroundings, a safe and healthy place to be.
Toolbox Talks
- Toolbox talks are informal group discussions that focus on particular safety issues within a working environment.
The purpose of toolbox talks are to:
- Promote safety awareness
- Introduce workers to new safety rules, equipment and workplace practices
- Help when reviewing new laws or industry standards
- Encourage workers to discuss their experiences regarding health and safety issues
Committee Meetings
- A Health and Safety committee enables Employers and Employees to communicate on matters related to Health and Safety, by having Employer Representatives and Health and Safety Representatives meet regularly (at least every 3 months), and work together to develop policies and procedures to improve work-related Health and Safety outcomes.
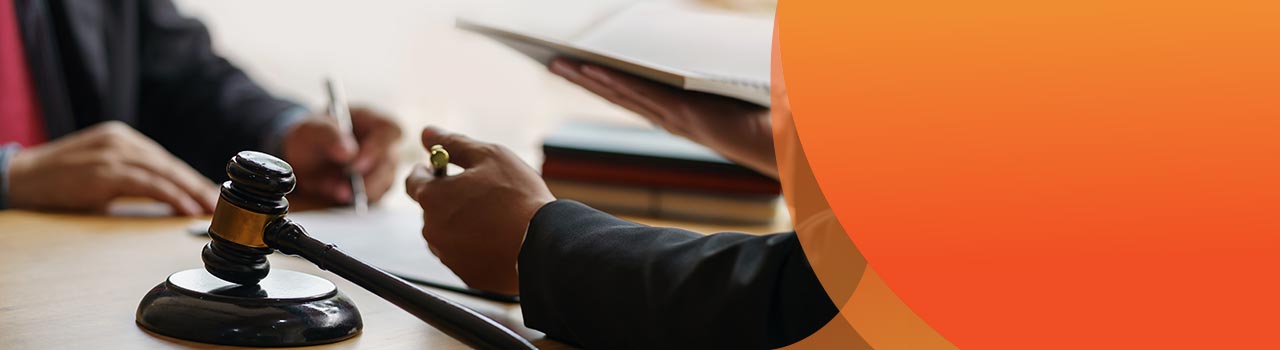
OHS Legal Appointments
- Employers need to make specific legal appointments in accordance with the OHS Act in order to ensure legal compliance. It is important to describe exactly what it is that the employee is expected to do in appointment letters, while it must also be ensured that the employee is qualified and ready to take on a job.
SOP
- A Safe Operating Procedure, also known as a Safe Work Procedure is a working risk control document that describes the safest and most efficient way to perform a task. It therefore not only looks at the protection of the operator/employee but also the quality of the product, process or service being created. The document generally lists the associated hazards involved in performing a task, what risk score (according to the applicable risk matrix) is associated with the hazards, what personal protective equipment is required, and the steps involved to complete the activity without incident.
The document could be split up to meet the above requirements as follows:
- The Steps involved
- The Hazards involved
- The inherent risk
- The control measures
- The possible residual risk.
The SOP must be reviewed annually and all operators must receive training on the applicable SOP to perform work safely.
OHS Policy
- A Health and Safety Policy is a written statement of principles and goals explaining the company’s commitment to workplace Health and Safety. Reviewing the policy over time to make sure it is still effective is an important duty as it shows management's commitment to workplace Health and Safety.
OHS Risk Assessment and Control Measures
- A risk assessment is the process where you:
- Identify hazards.
- Analyze or evaluate the risks of the hazards
- Determine appropriate ways to eliminate or control the hazard.
A Health and Safety Risk Assessment is one the most important parts of the Occupational Health & Safety program, no company can be compliant to the OHS Act if this is not conducted and monitored on a regular basis. The Risk Assessment must be conducted by a Risk Assessor who has be properly trained.
Keeping your workplace legally Health and Safety Compliant may seem like a daunting task. At MAKROSAFE, we have an experienced team of OHS experts available to assist in keeping your company Health and Safety Compliant according to South African Health and Safety Acts and Regulations.
Keeping your workplace legally Health and Safety Compliant may seem like a daunting task. At MAKROSAFE, we have an experienced team of OHS experts available to assist in keeping your company Health and Safety Compliant according to South African Occupational Health and Safety Act 85 of 1993 and Regulations.
The MAKROSAFE Health and Safety Risk Control Package will assist you with your Risk Management Programme.
By signing up with our Health and Safety Risk Control Package, MAKROSAFE will assist you with your Risk Management journey.
Copy of the OHS Act
- It is important for every employer with five or more persons in his employment to have a copy of the Occupational Health and Safety Act 85 of 1993 and relevant Regulations available at the work place so that they can understand the importance of compliance as well as make their work environment Safe and Healthy for themselves and their employees around them. It is also mandatory to have the Act mounted as a wall chart.
Click on the image below to find a SafetyWallet Solution that suits your business (branch specific) and get the 21 benefits along with the subscription:
Comments (14)
Can I get help with OHS COMPLIANCE
2021-07-06 10:31:51can i get assistance to do OHS training
2022-11-28 12:16:36Very good...is the "Audit-Template" available to purchase as an "app" under licence ??
2018-06-10 22:10:35I like to do safety certificate
2020-01-07 17:12:45very nice submit, I definitely love this website, keep on it .
2022-07-21 19:32:20Excellent Health and Safety Compliance tips
2016-07-16 07:48:15How to advise on ohs compliance
2020-10-11 02:51:15How to advise on ohs compliance
2020-10-11 02:51:19Congratulation health and safety I like that
2016-11-09 22:12:04I am impressed with your approach and also the wonderful tips and systems that you propogate. Let's hope that more top and senior management take note of the importance and benefit of complying with the legal requirements and the sometimes disastrous results that lead from 'looking the other way'.
2022-05-18 16:39:40You are doing an amazing job. People nowadays forget the safety of employees and focus more on the production side. Companies wants to safe money at the expense of employees health. Health and safety representatives becomes null and void in some companies. With Covid in our midst one expects more health and safety reps surfacing and regard their job as important. Perhaps you should start outsourcing and make your survices available for all COMPANIES, seeing that SA trained OHS reps are all leaving for overseas jobs
2022-05-21 19:51:42Quote for OHS Compliance certificate for new training academy.
2021-10-05 14:39:12good look
2022-10-10 10:16:44In this analysis, I am going to provide you with a fast Carbon Fiber Hard Hat. In order that while choosing a troublesome hat you will stay behind well-aware of each feature of a troublesome hat. Carbon fiber hard hats are an area of daily PPE (Personal Protective Equipment) a lot of persons need to be dressed in the workplace.
2022-10-15 11:05:20