Monitoring the compliance of workplace safety and health requirements must be conducted. However, when monitoring is conducted the results of the monitoring must be compared with some standard or requirement. If this comparison is not done, then monitoring will only be done for monitoring sake and nothing else. Monitoring must therefore be done and simultaneously a mental comparison drawn between what is being seen, heard and felt and what actual requirements are. This mental comparison will then be converted into written notes which will then form the basis of formal action, by management, who is responsible to address any problem areas.
Specific Requirements for monitoring compliance
The concept of “monitoring” was explained in section 1.4. In this section, however, two further considerations are highlighted. These two main considerations are:
- Why do we monitor?
- What do we require in order to monitor?
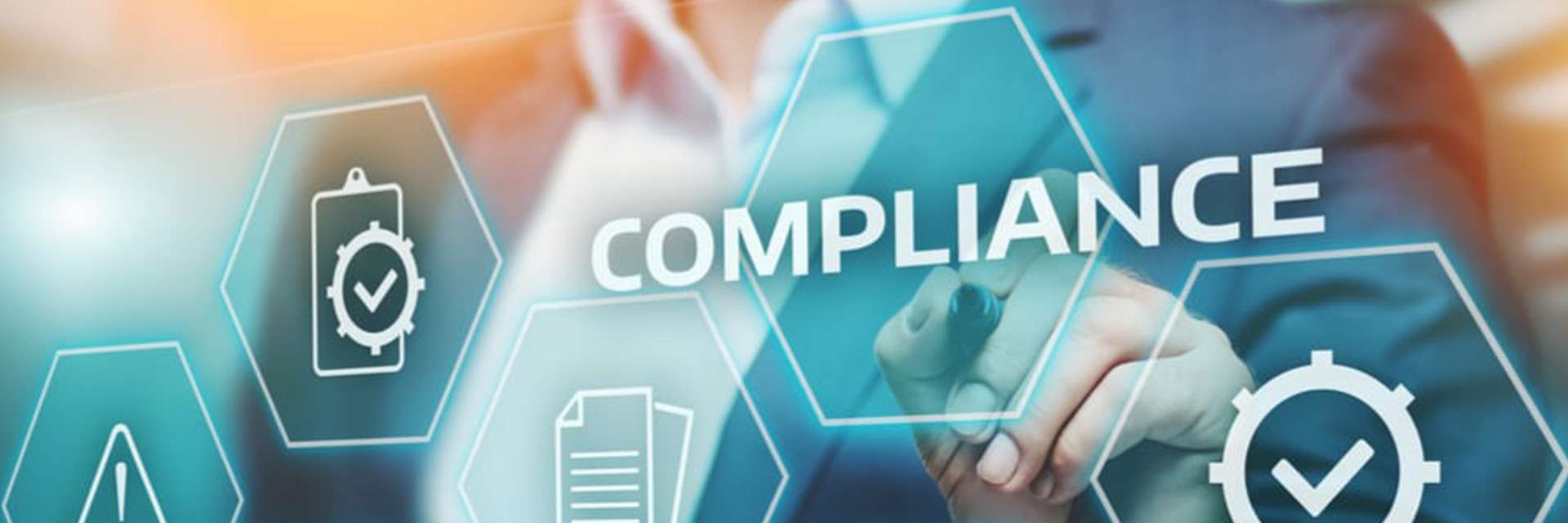
Why Do We Monitor?
Workplace health and safety issues are monitored so as to ensure a pleasant, safe, healthy and environmentally friendly workplace which satisfies the rights of workers (in terms of the country’s Constitution and labour laws of which the OHS Act is a part) and which contributes to the productivity and success of the organisation itself. This was explained in detail.
What do we require in order to monitor?
In order to monitor occupational health and safety matters correctly, an organisation requires the following:
- Knowledge of the laws of the country in order to understand exactly what is required, of an employer, by these laws.
- That all employees know and understand that they also have responsibilities in terms of the law.
- An organisational workplace health and safety policy.
- An organisational workplace safety, health and environmental management system which caters for the identification, informing, corrective action and continual improvement of occupational health, safety and environmental matters.
Human resources (i.e. employees) who will do the actual monitoring. As mentioned above, these people will come from the ranks
All employees.
The Chief Executive Officer / Owners of the organisation as represented by appointed and delegated managers.
Health and safety representatives.
Health and safety committees.
Inspectors from the Department of Labour.
The supporting technical equipment needed to fully apply thorough safety, health and environmental monitoring. The various possible types of equipment required to do this will be explained in detail below.
Purpose and Extent of Monitoring
Implementing an OHS management system does not in itself guarantee success. To ensure that risks are controlled effectively, there should be a system in place to measure and evaluate OHS performance and take preventative and corrective action where appropriate.
Regular measurement and evaluation will enable an organisation to see what is working well and what is not; and develop strategies to remedy any problems and include these in the planning process. Management should ensure that corrective and preventative actions are followed up to ensure they are implemented and effective.
Performance measurement needs to strike a balance between actively monitoring the OHS management system and reactively assessing failures.
The Purpose of Monitoring and Maintaining Health and Safety Issues
The purpose of monitoring workplace requirements is to make sure that all legal and best practice safety, health and environmental requirements for a particular workplace are in place and remain in place. Monitoring is a vital part of a health and safety culture. Occupational Health, Safety and Environmental management systems must allow decision-makers to receive both specific (e.g. incident-led) and routine reports on the state or health, safety and environmental workplace issues.
Much day-to-day health and safety information, obtained through the monitoring activity, need be reported only at the time of a formal review. But only a strong system of monitoring can ensure that the formal review can proceed as planned – and that relevant events in the interim are brought to management’s attention.
Because monitoring, as part of the employer’s legal responsibility, is so important, the following considerations must be realised:
Appropriate weight is given to reporting both preventive information (such as progress of training and maintenance programmes) and incident data (such as accident and sickness absence rates).
Periodic audits of the effectiveness of management structures and risk controls for health and safety are carried out.The impact of changes such as the introduction of new procedures, work processes or products, or any major health and safety failure, is reported as soon as possible to management.
There are procedures to implement new and changed legal requirements and to consider other external developments and events.
Best practice in workplace monitoring requires that:
Effective monitoring of sickness absence and workplace health can alert management to underlying problems that could seriously damage performance or result in accidents and long-term illness.
The collection of workplace health and safety data can allow management to benchmark (i.e. compare) the organisations performance against others in its sector.Appraisals of senior managers can include an assessment of their contribution to health and safety performance.
Management can receive regular reports on the health and safety performance and actions of contractors.Some organisations have found they win greater support for health and safety by involving workers in monitoring.
The Extent of Monitoring That Should Take Place in Any WorkplaceThe extent of this monitoring includes the internal operations of the whole workplace, customers, contractors, the local community and the environment.
All management members and employees (especially occupational health and safety representatives) tasked with occupational health, safety and environmental matters will use certain resources to monitor workplace safety, health and environmental issues. The primary resources (or tools) used will be:
Observation (eyesight for watching out for occupational health, safety and environmental issues).
Listening (listening for signs of safety hazards, especially with fast moving machinery).
Touching (to detect heat or vibration).
Interviewing (asking questions).
Recording (noting problem, or non-conformance, issues).
Freedom of Movement for OHS Representatives and Inspectors
In order to fully monitor workplace occupational health, safety and environmental requirements, all the people involved in this monitoring must have the necessary freedom of movement in order to access all places of work on the organisations’ premises.
Monitoring Equipment
In order to monitor occupational health, safety and environmental requirements specialised monitoring equipment will often have to be use. This equipment covers a vast scope of possible testing (or monitoring) and can focus on many issues, viz:
- Balancing equipment for rotating machinery.
- Air quality testing for dust, oxygen levels and toxins.
- Temperature readings.
- Smoke detection.
- Acidity testing.
- Fume detection.
- Human stress level monitoring.
- Distance measurement.
- Alignment equipment (e.g. laser beams).
- Vibration measurement.
- Noise level measurement.
- Measuring high or low lighting levels.
Occupational Health and Safety Training
All workers have the right to be informed, the employer must see to it that every worker is informed and clearly understands the health and safety hazards of any work being done, anything being produced, processed, used, stored, handled or transported, and any equipment or machinery being used.The employer must then provide information about precautionary measures against these hazards. The employer must inform health and safety representatives when an inspector notifies him or her of inspections and investigations, to be conducted at the premises. Employee assistance programmes need to incorporate all relevant disease control training and awareness for example: HIV/AIDS training, TB etc.
Training methods for the workers working on the jobsite:
- The work plan must be specific to the work site.
- The work plan must be available on the work site for review.
- The documentation of training must be available on the work site for review.
Using Specialist Contractors
In many cases organisations do not wish to purchase specialised equipment (which is normally very expensive) or employ occupational health, safety and environmental testing specialists themselves (which is also very expensive). In order to do this a process called “out-sourcing” is used. Out-sourcing simply means that contractors are used to provide services when and where they are needed. These contractors are then paid only for the time that they are actually working on the organisation’s premises. The use of out-sourcing is a very popular, and growing and is a world-wide trend.
Work Specific Checklists
It is the responsibility of the employer to create and maintain an occupational health, safety and environmental system. A very effective way to do this is to provide all personnel involved in the monitoring of occupational health, safety and environmental requirements with detailed checklists.
For all your Occupational Health and Safety needs, kindly click on the picture below:
Comments (1)
Very detailed and informative SHE monitoring management system. Please include implementation of SHE management systems.
2023-01-25 21:41:35Dear Musa Thank you for your request via our comments... Please follow this link and sign up with The Health and Safety Risk Control Package: https://www.makrosafe.co.za/Health-and-Safety-Risk-Control-Package
2023-03-06 08:25:14